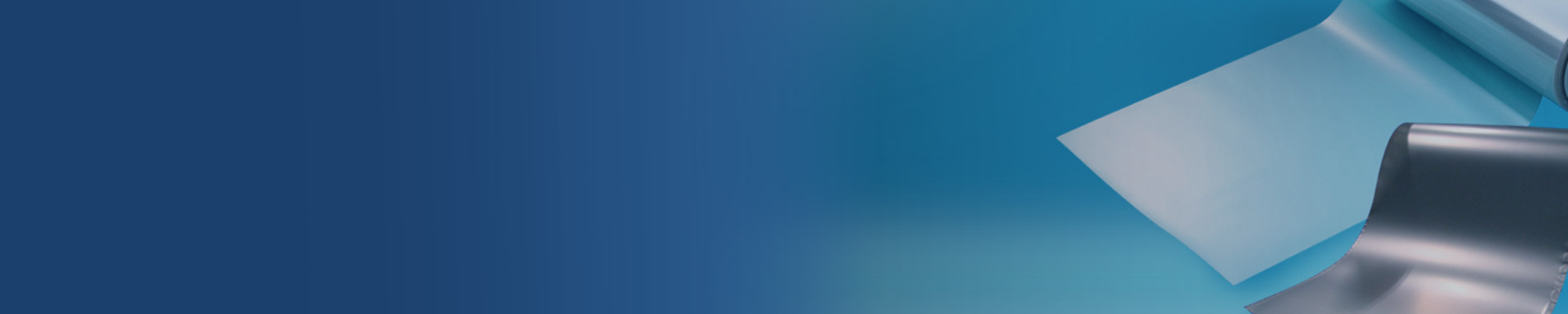
Specialized Laminating
- TOP
- Products and service
- Processing and services
- Specialized Laminating
Composite technology and specialized lamination
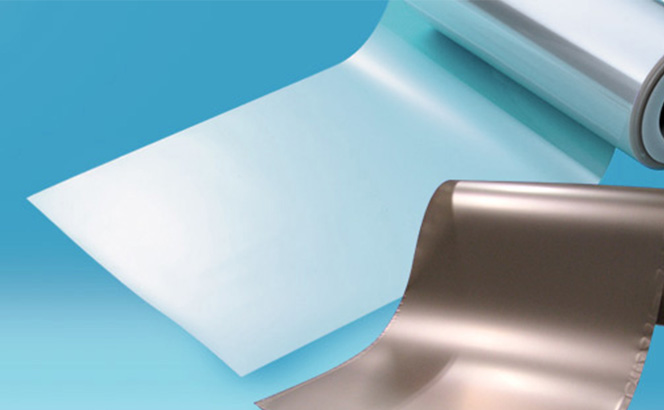
We propose new functional film by lamination of plastic film and metal foil, or with thermal lamination and other surface coating,
We can match customer's needs by our high technology even the materials are in difficult composition.
Major initiatives INITIATIVES
PANAC provides both Dry Lamination by laminating materials with adhesive and Thermal Lamination by heat melting on the film surface.
By laminating two or more layers of film or foils, utilizing the characteristics of each material, it is possible to exert the performance which can not be responsible by itself.
In addition, we melt resins and coat them to materials, or combine special processing such as surface embossing, we propose optimum products and processing processes that meet customer needs.
-
Adoption track record
Shielding parts, damping parts, backlight parts·FPC·medical parts and electronic parts or materials, etc.
Secondary processing after the laminate: Slitting or Cutting or Punching is here.!
Dry lamination
The process can apply adhesive to plastic films, and bond it to the other films after dried.
Different materials can be bonded together such as plastic film and metal foil.
Processing specification | Coating section cleanness | class 1000、10000 | ||
Use material width | max 1700mm | |||
Use material type | 各Various plastic films , metal foil | |||
Adhesive coating thickness(Dry) | 0.1μm~100μm ※2 heads continuous coating is possible ( undercoating + coating ) |
|||
Characteristic |
|
|||
Material usage records | Various engineering plastics (PET, PEN, PI, PPE , etc.) , olefin film (PE, OPP, TPX , etc. ), PMMA, TAC, other plastic SUS foil (12 ~ 100μm), Cu foil (12 ~ 70μm), Al foil (9 ~ 200μm), Ti foil , Fe foil etc. |
|||
Adhesive | We can design adhesives to meet customer's requirements and applications.Modulus control (Curl tracking and control the stretch of the substrate) Chemical resistance (etching resistance) Adhesive force control (ensure the adhesive force between various materials) Functionality grant (rust prevention, antistatic etc.) |
|||
Working process | ![]() |
|||
Composite configuration example | Metal foil / PET composite product , olefin / PET composite product , metal foil / metal foil composite product |
Thermal lamination
Without using any adhesive, melt the material such as a plastic film by heat, and bond by pressure bonding process. Materials that could not be boned by dry lamination can also be processed.
Since the laminated product without adhesive layer, able to exert a material inherent properties (heat resistance, etc.).
Processing specification | Laminating unit cleanliness | class 10000 | ||
Use material width | max 1400mm | |||
Use material type | Various engineering plastics (PET, PEN, PI, PPE, fluorine film, etc.) , olefin-based filmSUS foil (10 ~ 100μm), Cu foil (12 ~ 70μm), Al foil (9 ~ 200μm), Ti foil , Fe foil etc.Hot melt sheet , fabric sheet, etc. |
|||
Heating temperature | max 400℃ | |||
Characteristic |
|
|||
Material use performance | Various engineering plastics , olefin film , fluorine film , LCP film , glass cloth , etc. Metal foils , SUS, Cu, Al, Ti , etc. |
|||
Composite configuration example | Metal foil / plastic film composite article (SUS / thermoplastic PI, SUS / PEN , etc.) High heat-resistance film composite products (PI / fluorine film ) Multilayer products ( olefin-based film / fluorine film / olefin-based film, etc.) Fabric sheet composite products ( glass cloth / fluorine film, etc.) |
Special processing
Resin melt coating processing
Coat or bond directly to the material while melting the hot-melt resin.
Resin melt coating processing |
|
Processing combination example | 1.Film / hot melt resin 2.Metal foil / hot melt resin 3.Fabric substrate / hot melt resin |
Decorative machining (Embossing on films surface)
Embossing onto the film surface.
Characteristic |
|